This week, Mataró has been unanimously elected as the new president city of the European…
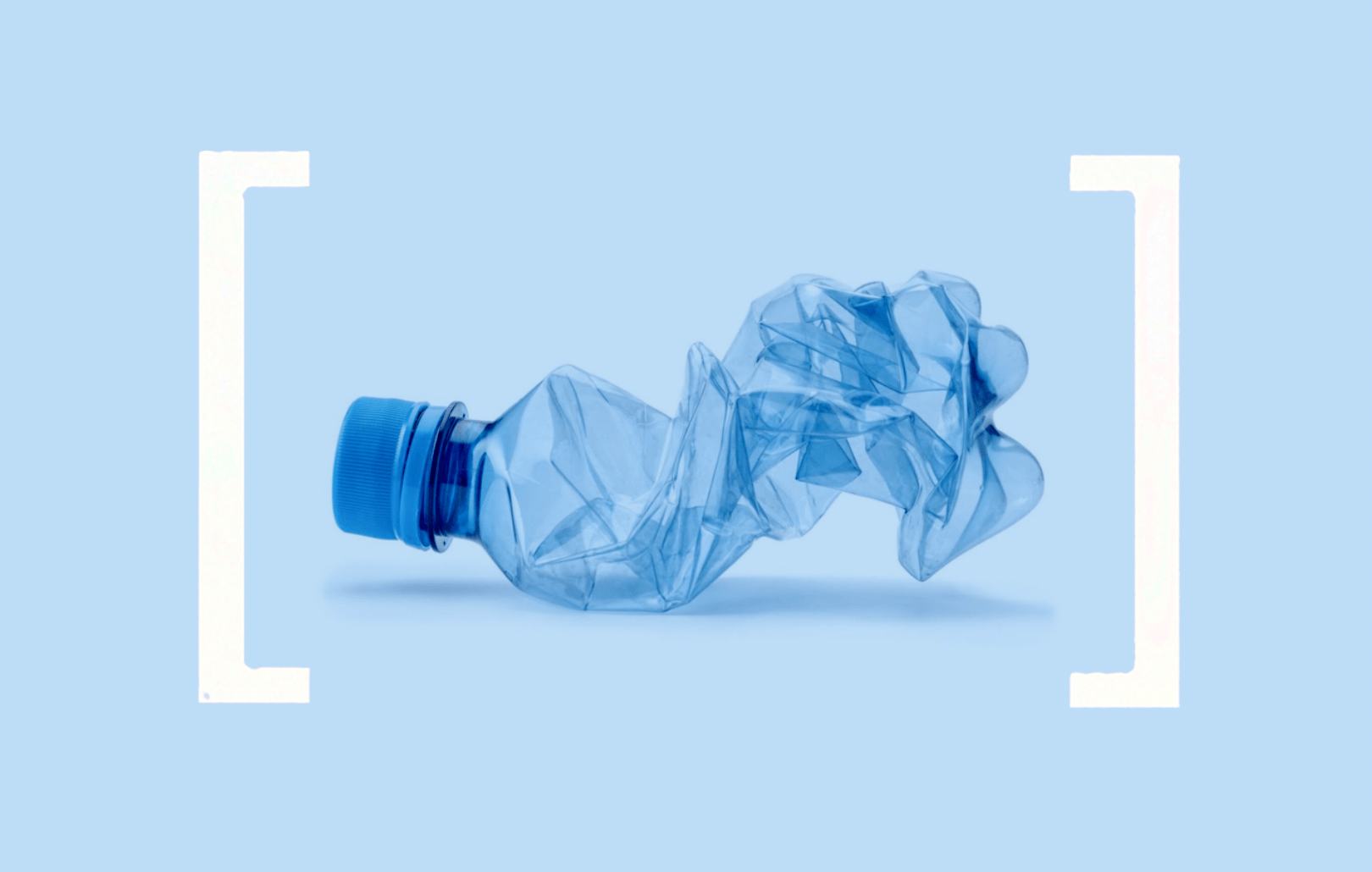
The Revolution of Sustainable Technical Fabrics in the Personal Protection Industry
A Step Towards Sustainability in Protective Textiles
The textile industry specializing in official protection and technical fabrics is moving towards sustainability by producing innovative materials from post-consumer plastic. This technique not only helps reduce plastic waste but also drives the circular economy and minimizes the carbon footprint in the manufacturing of technical equipment and safety uniforms.
Thus, the textile industry is undergoing a significant transformation towards sustainability, with companies like C.P. Aluart leading this change by producing technical fabrics from post-consumer recycled plastic. This initiative not only reduces plastic waste but also promotes a circular economy and decreases the carbon footprint of textile production.
Every year, millions of tons of plastic end up in landfills and oceans. However, leading companies in the sector have found an opportunity in this waste to transform it into high-quality textile fibers used in personal protective equipment (PPE), military, police, and industrial clothing. “The use of recycled plastic in technical fabrics is not just an innovation but a necessity to ensure a more sustainable and efficient future,” say textile development experts.
Commitment to Sustainability
C.P. Aluart, a specialist in technical fabrics and personal protective equipment, has integrated sustainability into the core of its business strategy. They use fibers such as COOLMAX® EcoMade, derived from the recycling of post-consumer plastic bottles, to create products that offer high breathability and moisture control without compromising environmental respect.
Benefits for the Environment and Occupational Safety
The textile recycling process reduces water and energy consumption compared to the production of virgin fibers such as conventional polyester. Additionally, it decreases reliance on fossil resources and CO₂ emissions, improving the environmental impact of the official protection textile industry.
Companies specializing in technical fabrics have implemented materials like COOLMAX® EcoMade, made from recycled plastic bottles, to manufacture highly breathable and comfortable clothing. These advances enhance worker safety in critical sectors such as construction, public security, and the military industry, without compromising the durability and resistance of the materials.
The Future of Recycled Technical Fabrics
As environmental regulations tighten and sustainability awareness grows, more companies are seeking responsible alternatives for manufacturing their protective equipment. The recycled fabric market is expected to continue expanding, with innovations improving recycling efficiency and increasing the variety of reusable plastics in textile production.
Recycling plastic in the official protection textile industry is not just an ecological solution but a necessary evolution to ensure safety, comfort, and environmental commitment in the sector.